






ENGINEERING
AND CREATIVE
SERVICES
Conceptualizing Your
Idea With Visuals
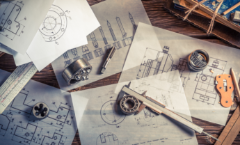
LOCATIONS
CORPORATE OFFICE
3 MILLTOWN COURT
UNION, NJ 07083
(+1) 800 631 7392
O.BERK® OF NEW ENGLAND
300 CALLEGARI DRIVE
WEST HAVEN, CT 06516
(+1) 888 653 6657
O.BERK® | KOLS
10001 FRANKLIN SQUARE
DRIVE
SUITE D
NOTTINGHAM, MD 21236
(+1) 410 646 2300
O.BERK® WEST
13918 EQUITABLE ROAD
CERRITOS, CA 90703
(+1) 562 802 0515